www.revista-fabricacion.com
27
'21
Written on Modified on
AUTOMATIZACIÓN DEL CAMBIO DE PLANTILLAS Y PASTA DE SOLDADURA PARA AUMENTAR LA PRODUCTIVIDAD DEL MONTAJE SUPERFICIAL
Las empresas de fabricación de productos electrónicos de hoy en día, ya sean OEM u ODM/EMS, necesitan ser capaces de manejar tipos de componentes desde los chips SMD más pequeños hasta los semiconductores de gran tamaño, así como componentes inusuales como los conectores de gran tamaño montados en agujeros pasantes. Además, los frecuentes cambios de producto son un reto común y deben completarse de la forma más rápida y eficiente posible.
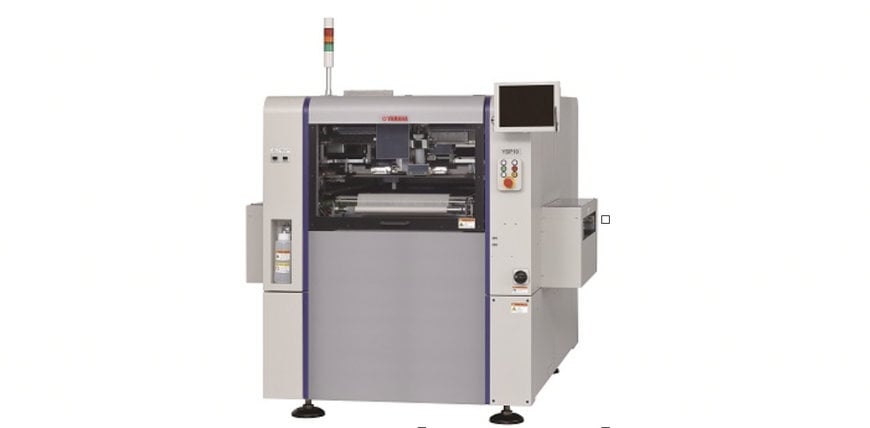
Acelerar el cambio de producto
Cuando se ensamblan placas a alta velocidad en una línea de montaje superficial, y en escenarios de fabricación que implican muchos cambios al día, la automatización de tantas tareas de cambio de producto como sea posible puede ayudar a ahorrar tiempo y evitar errores humanos que, de otro modo, causan pérdidas de producción y exigen tiempo extra para rectificar. Un sistema útil como el de cambio automático de programa (APCO) puede realizar el cambio de programa rápidamente y garantizar que se cargue el programa correcto en todas las máquinas de la línea. En cuanto a las montadoras de componentes, es posible configurar alimentadores para gestionar varios productos sin necesidad de cambiarlos. Cuando se necesita una nueva configuración del alimentador, ésta se puede configurar fuera de línea y los alimentadores se incorporan a la máquina justo a tiempo para el cambio. Los alimentadores de cambio automático pueden entonces encargarse de empezar a suministrar los nuevos componentes a la máquina.
El cambio de la impresora serigráfica es un procedimiento más complicado que suele implicar la retirada de la pasta de la plantilla (stencil), su limpieza, la retirada y sustitución de la plantilla, la reconfiguración de las clavijas elevadoras y el reajuste de la espátula (squeegee). La figura 1 describe la secuencia completa de acciones necesarias. Para completar el cambio, el montaje debe detenerse y no puede reanudarse hasta que se completen todas las acciones. El proceso completo puede durar entre 10 y 15 minutos, como se indica.
Entre estas tareas, procedimientos como la retirada y la sustitución de la plantilla suelen requerir que el operario reciba formación para realizar las tareas de forma satisfactoria. Por lo general, la automatización de las tareas intensivas en mano de obra asociadas a un cambio de impresora ha resultado compleja y difícil. Ahora, gracias a una importante reingeniería de la estructura interna de la impresora serigráfica estándar, Yamaha ha creado la nueva YSP10 (figura 2), ganadora del premio Global SMT, con capacidades de cambio automatizado que incluyen el intercambio de plantillas, el intercambio de clavijas elevadoras y la retirada y sustitución del rollo de pasta de soldadura en la siguiente plantilla.
Todo el proceso de cambio puede completarse en 3-5 minutos y la producción puede reanudarse inmediatamente sin necesidad de realizar más comprobaciones, ajustes o acondicionamiento de la pasta de soldadura. La secuencia mostrada en la figura 3 muestra cómo se ha reducido significativamente el tiempo para completar el cambio.
Una combinación de lo nuevo y probado
El cabezal 3S (swing single squeegee) de Yamaha (figura 4) permite optimizar el ángulo de la espátula de goma mediante un servoajuste para garantizar un llenado óptimo de la abertura. Se sabe que el ángulo de la espátula tiene un mayor efecto en el llenado de la abertura que otros parámetros como la velocidad y la presión de la espátula. En particular, cualquier disolvente que pueda estar presente en la superficie de la plantilla inmediatamente después de que se haya completado un ciclo de limpieza puede causar depósitos de soldadura defectuosos en las primeras placas que se impriman cuando se reanude la operación. La impresora tiene un sistema de ajuste de llenado que cambia automáticamente el ángulo de la espátula para compensar las diferencias de llenado debidas al disolvente. Esto ayuda a prevenir los defectos de impresión sin requerir una acción adicional o un retraso en el secado de la plantilla.
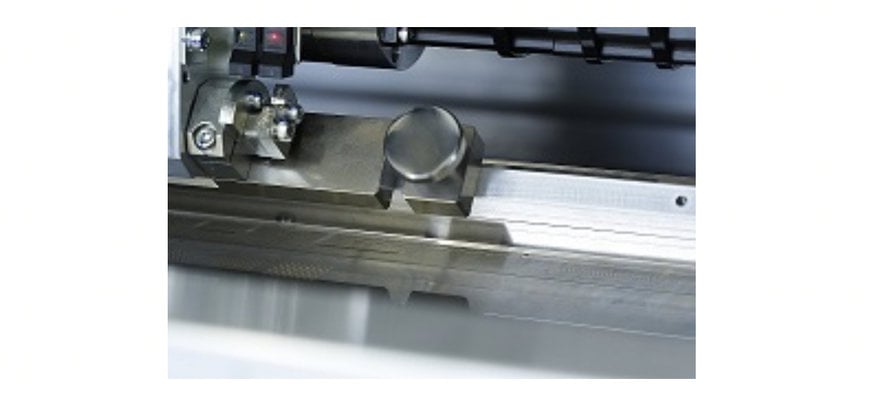
El cabezal 3S permite optimizar automáticamente el ángulo de la espátula
El diseño del cabezal funciona con una tecnología única de espátula que cuenta con una cuchilla flexible de sólo 100 micras de grosor tratada con un revestimiento de baja fricción de 10 micras idéntico al que se aplica a las paredes de los cilindros de los motores de motocicletas de alto rendimiento de Yamaha para minimizar el desperdicio de energía y prolongar la durabilidad. Este revestimiento elimina eficazmente el desgaste de la espátula y de la plantilla, lo que no sólo contribuye a mejorar la repetibilidad, sino que también ayuda a garantizar mejores resultados cuando se imprime con plantillas escalonadas, así como a reducir el coste global de propiedad del proceso de impresión.
Los efectos combinados de la espátula y el cabezal 3S permiten obtener resultados superiores cuando se realizan procesos como el pin en pasta. La impresora puede rellenar los agujeros de la pasta de impresión (PTH) con una sola pasada de la espátula, mientras que otros sistemas que tienen un ángulo fijo y una cuchilla rígida pueden necesitar hacer varias pasadas. Las empresas que necesitan garantizar un pegado eficaz de los pines cuando construyen conjuntos que contienen, por ejemplo, grandes conectores de automoción con agujeros pasantes de varios pines, aprecian el ahorro de tiempo y la mejora de la calidad y la repetibilidad que puede ofrecer este sistema.
Con el rediseño de la disposición interna de la impresora para permitir el cambio automático de la plantilla, el mecanismo de sujeción de la plantilla asistido por vacío de Yamaha ayuda a garantizar una alta precisión posicional y repetibilidad. El vacío, aplicado a la parte metálica de la plantilla, elimina los efectos de cualquier distorsión en el marco de la plantilla y también minimiza cualquier inexactitud que pueda resultar de la elongación de la malla al pasar la espátula. La capacidad de impresión y la estabilidad de las formas de depósito de la soldadura aumentan. Además del mecanismo de sujeción, el sistema gráfico de alineación visual de la impresora ayuda a alinear rápida e intuitivamente la plantilla y la placa, lo que permite una alineación perfecta de la placa con la plantilla incluso cuando las referencias son deficientes o no están presentes.
Características como el auto pin teach se han consolidado en las últimas generaciones de máquinas de serigrafía. Estas funciones simplifican la generación de programas, ya que determinan automáticamente las posiciones óptimas de las clavijas para proporcionar soporte durante la impresión, utilizando información CAD como los datos gerber o utilizando una imagen digital de alta resolución de la placa. El conjunto de herramientas que permiten los cambios automatizados añade ahora el intercambio automático de pines a las capacidades de la impresora, lo que simplifica aún más la configuración de los pines de las herramientas para dar soporte a la nueva placa.
La manipulación del rollo de pasta de soldadura también está automatizada para eliminar las ineficiencias al tratar con la pasta de soldadura restante en la plantilla en el momento del cambio. La pasta se retira automáticamente de la plantilla y se retiene, manteniendo la pasta en forma de rollo. La pasta se puede volver a depositar en la nueva superficie de la plantilla después del cambio. Antes de reanudar la impresión, se mide el diámetro del rollo de pasta y se añade pasta de soldadura adicional si es necesario, según el sistema de control de estabilidad de la impresión (PSC). Esta secuencia ofrece dos ventajas principales: se elimina el contacto del operario con la pasta y no se pierde tiempo en acondicionar el rollo de pasta recién cargado. La impresión puede continuar inmediatamente, utilizando el nuevo programa, en cuanto la primera placa del nuevo lote entra en la máquina. El sistema PSC mide con frecuencia el diámetro del rollo de pasta durante el funcionamiento normal de la impresora, lo que contribuye a la repetibilidad del proceso al ayudar a garantizar un llenado consistente de las aberturas.
Inspección precisa incorporada
Un usuario de la impresora YSP10 con sede en Bélgica, que opera una línea de producción dedicada a los ensamblajes de automóviles, descubrió que el sistema de inspección bidimensional integrado en la impresora mostraba una precisión comparable a la de un sistema de inspección de pasta de soldadura (SPI) dedicado en 3D. Por lo tanto, este sistema 2D integrado (figura 5) puede garantizar resultados fiables de inspección de la pasta de soldadura dentro del tiempo de ciclo estándar de la impresora. Con su campo de visión (FOV) de 30 mm x 22,5 mm, y con una resolución de 18,7 µm, este sistema puede identificar defectos de impresión en patrones de depósito finos para componentes como pequeños chips SMD y BGA de 0,5 mm de paso. El sistema proporciona información automática para activar la limpieza de la plantilla si se detectan problemas relacionados con la pasta.
Conclusión
Las tareas asociadas a los cambios de impresora de pantalla han sido históricamente las más difíciles de automatizar. Mientras que los aspectos posteriores, como el montaje y la inspección, se han beneficiado de una automatización, el cambio de la impresora serigráfica ha seguido siendo una tarea de gran intensidad de mano de obra llevada a cabo por el operario. Esta última frontera ha sido conquistada, permitiendo la automatización de las tareas de cambio de producto asociadas a todas las máquinas de la línea de montaje superficial, lo que se traduce en una mayor productividad y calidad.
www.yamaha-motor-im.com