www.revista-fabricacion.com
19
'20
Written on Modified on
PRUEBAS DE ERROR DE CALIBRACIÓN DE LA REGLA LINEAL CON EL INTERFERÓMETRO LÁSER
Para conseguir una precisión de medición uniforme por debajo de la micra, un sistema de calibración automática de la regla lineal desarrollado por Standards and Calibration Laboratory (SCL) de Hong Kong, ha convertido la compensación de errores automática en el principal criterio de diseño. Se utilizó un interferómetro láser XL-80 y la unidad de compensación XC-80 de Renishaw para gestionar las fuentes de error Abbe y los cambios de las condiciones ambientales.
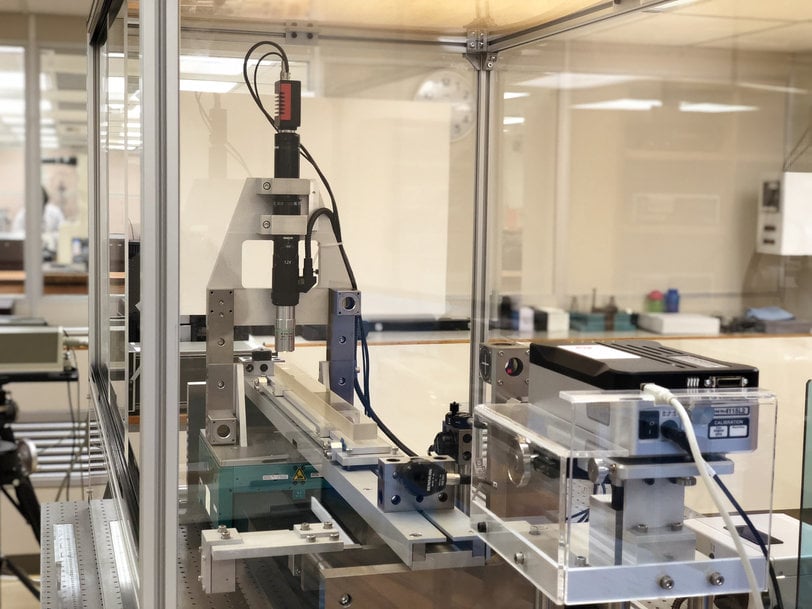
Historial
Las reglas lineales de precisión se desarrollan a menudo en equipos de medición de longitud de alta precisión, que incluyen comparadores, microscopios e instrumentos de exploración mecánica, para proporcionar una referencia exacta para medir con precisión distancias o recorridos. Generalmente fabricadas en cristal, las reglas lineales llevan grabadas en la superficie líneas paralelas equidistantes perpendiculares al eje de la regla de línea. Para medir y verificar las distancias entre las graduaciones de la regla de línea, se necesitan instrumentos de alta precisión.
El laboratorio Standards and Calibration Laboratory, parte de la comisión Innovation and Technology Commission de la Región Especial Administrativa de Hong Kong, es el responsable de formular y mantener los estándares de referencia de medición física de la región de Hong Kong. Facilita servicios de calibración a los usuarios locales de estándares e instrumentos de medición, de forma que puedan realizar sus tareas de medición con precisión y hacer un seguimiento correcto de su trabajo conforme a los estándares correspondientes.
SCL se impuso la tarea de diseñar y fabricar un nuevo sistema de calibración de reglas lineales automático, con capacidad para obtener precisiones de medición por debajo de la micra. Pero, lo más importante, tendría que compensar automáticamente los errores Abbe provocados por desplazamientos angulares mínimos de los equipos y cualquier variación de las condiciones ambientales.
Retos
Según Ernst Abbe de Zeiss en 1890, el Principio Abbe se define como ‘el principio de alineación’ y establece: “Si es necesario evitar los errores de paralaje, el sistema de medición debe instalarse coaxialmente (es decir, alineado con) la línea en la que se va a medir el desplazamiento (longitud dada) en la pieza de trabajo”.
El error Abbe se introduce, por tanto, cuando el punto que se va a medir está separado lateralmente del eje de medición y el sistema de posicionamiento está sometido a movimiento angular. Esto hace que el desplazamiento medido aparente ser más corto o más largo que el desplazamiento real. La separación espacial del punto medido y el eje de medición se denomina compensación de Abbe. A modo de ejemplo sencillo, pruebe a medir un calibre. Entre el eje de la regla y el eje de medición (formado entre las puntas) existe una compensación de Abbe. Cualquier fallo de rectitud, cuadratura u ‘holgura’ del calibre, generará un movimiento angular en las puntas y, por tanto, un error Abbe.
J.B. Bryan, que definió el Principio Abbe como “el primer principio de diseño de máquina y metrología dimensional”, continuó hasta restablecerlo en términos de máquina como: “El sistema de medición de desplazamiento debe estar alineado con el punto funcional cuyo desplazamiento se va a medir. Si esto no es posible, las guías que transfieren el desplazamiento deben carecer de movimiento angular, si no, deberán utilizarse datos de movimiento angular para calcular las consecuencias de la compensación”.
En resumen, para medir la precisión de las graduaciones de una regla de línea, se mide la distancia entre una línea de referencia (generalmente la posición cero) y la graduación objetivo. A continuación, es necesario aplicar el análisis de imagen y la tecnología de compensación, de forma que el sistema pueda calcular y ajustar las posiciones de lectura de la regla de línea y, por tanto, reducir en error Abbe.
No obstante, cuando se utilizan realmente estos sistemas, también es necesario considerar las influencias del mundo real y otras incertidumbres de diseño. Por consiguiente, es fundamental incorporar la compensación efectiva de los errores provocados por una serie de factores ambientales y humanos. En este caso, SCL se encuentra en el piso 35 de un edificio de 48, por lo que hubo que tener en cuenta, incluso, las vibraciones provocadas por el viento y el tráfico.
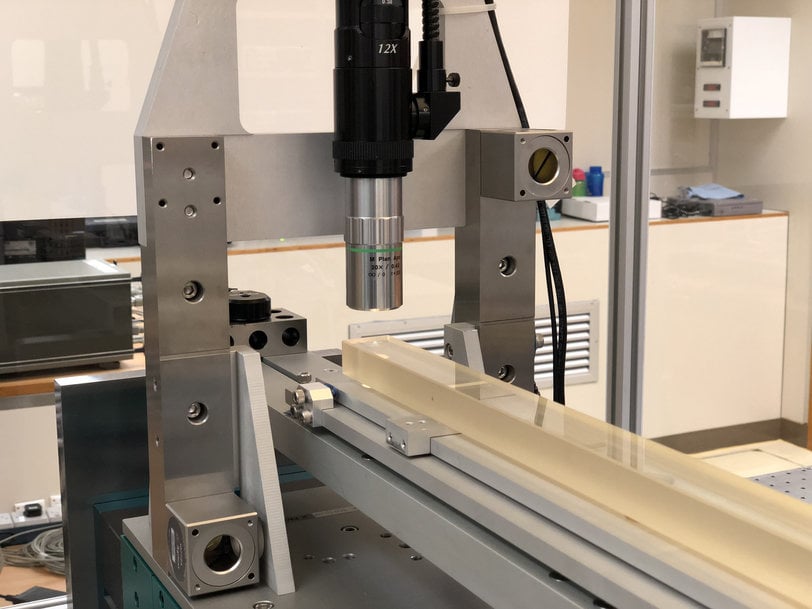
Automatización
Como respuesta a la entrada del operario, la plataforma deslizante se desplaza a la posición predeterminada para la medición de una línea objetivo. Cuando se detiene, el interferómetro láser lee los datos de posición y la cámara obtiene las imágenes de la regla graduada. A continuación, se analizan las imágenes para obtener la posición actual (según la distancia desde la posición cero del valor del pixel mostrado). La posición se compara con la posición calculada real y, a continuación, el sistema compensa la diferencia enviando instrucciones a la plataforma deslizante para ajustar la posición con precisión. A continuación, el interferómetro obtiene otra lectura de los datos de posición. El proceso completo se repite varias veces hasta que el error se encuentra en el rango de píxeles especificado y se obtiene la posición de la línea final.
Fuente láser estabilizada de precisión
El diseño del sistema utiliza el interferómetro láser XL-80 de Renishaw para compensar los errores Abbe en el sistema de medición relacionados con cualquier tipo de desplazamiento angular producido durante el reglaje. Podría estar relacionado con la linealidad de la plataforma deslizante, la colocación de la regla de línea o la posición del reflector, por ejemplo. Con una longitud de onda nominal de 633 nm, el interferómetro garantiza una precisión de medición lineal de ±0,5 ppm, gracias a una fuente láser estabilizada de precisión y una compensación ambiental precisa. Las lecturas se pueden obtener hasta 50 kHz, con una velocidad lineal máxima de 4 m/s y una resolución lineal de 1 nm, incluso a la máxima velocidad. Todas las opciones de medición se basan en mediciones de interferometría, que proporcionan más confianza en la precisión de los datos registrados.
El reglaje del interferómetro utiliza una configuración de medición lineal clásica. El rayo láser se divide en dos trayectorias al pasar por el desdoblador de haz S, donde una de las trayectorias forma un haz de referencia que pasa a través de la lente T y el reflector R de vuelta a la sonda de origen del láser, mientras que el otro, pasa a través de las lentes de transferencia T1, T2, T3 y el reflector R para crear un haz de medición de cambio de longitud. En el sistema SCL, se utilizó el XL-80 con la unidad de compensación XC-80. Las condiciones ambientales se miden en los sensores internos de presión y humedad del aire, con precisiones de 1 mbar y 6% respectivamente, además de tres sensores de temperatura del material y uno del aire, con una precisión de 0,1°C y 0,2°C respectivamente.
Solución
La distribución del sistema de medición de SCL se muestran en la Figura 1. Utiliza un método de desplazamiento en el que el dispositivo de medición recorre en un puente por encima de una regla lineal fija para medir la distancia entre una posición cero y una graduación de regla lineal. El conjunto completo se monta en una mesa con amortiguación de vibraciones flotante y, para un mejor control del perfil de temperatura, se protege en un recinto cerrado. La medición se realiza con un microscopio de alta resolución, una cámara CCD monográfica y un algoritmo de software de recuento de píxeles, montados en una plataforma deslizante de cojinetes de aire, accionada por un motor piezoeléctrico modo CA/CC. La plataforma deslizante del sistema alcanza una linealidad de 0,9 µm para un recorrido de medición de 800 mm y repetibilidad de 20 nm. Los valores máximos de giro, cabeceo y ladeo son de ± 0,5 arcosegundos cada uno.
Para compensar el error Abbe, el sistema SCL adopta s una construcción de aproximación, según J.B. Bryan. Bryan. En vez de usar datos de movimiento angular para calcular un valor de compensación, utiliza una ruta láser simétrica a ambos lados del eje de medición. De este modo, puede compensarse automáticamente cualquier movimiento angular detectado que pueda aumentar o reducir la lectura debido al error Abbe.
Resultados
SCL ha desarrollado con éxito un sistema automático de calibración de reglas de línea de alta precisión. Compatible con reglas de línea de hasta 750 mm de longitud, el sistema tiene una incertidumbre de medición de solo 0,15 a 0,41 nm. En el ensayo en el sistema, se utilizó una regla de cristal de 500 mm calibrada por el Korean Institute of Standards and Science (KRISS) como mecanismo de validación del sistema. Como mediciones, se seleccionó un total de 23 distancias entre las graduaciones de la regla y cero.
Los resultados de las mediciones se compararon con los valores obtenidos de KRISS. Todas las diferencias de los valores de medición se detectaron dentro de sus incertidumbres de medición individual y holgadamente dentro de la tasa de error normalizada de 0,7. En el sistema, la suma del error cuadrático de raíz del error Abbe, generado por los 5 segundos de arco de cabeceo y ladeo de la plataforma deslizante del microscopio en una distancia de 100mm puede calcularse en 3,4 µm. El análisis exhaustivo demuestra que con la integración del interferómetro XL-80, esta cifra de error Abbe se ha reducido en un 99%.
www.renishaw.com