www.revista-fabricacion.com
30
'09
Written on Modified on
Mejora de la calidad en las reparaciones por soldadura de defectos en el raíl con un coste reducido gracias a Tata Steel
Tata Steel Rail ha desarrollado una novedosa técnica para la reparación económica de defectos discretos en la superficie de rodadura del raíl. El principal punto fuerte de esta novedosa técnica consiste en la sustitución de aquellos aspectos del proceso convencional de tipo manual por arco metálico (Manual Metal Arc, MMA) que a menudo dan como resultado la variabilidad en la calidad de la reparación por operaciones automáticas y más controladas. El proceso semiautomático desarrollado emplea la soldadura de arco abierto con núcleo de fundente y recurre a una baja temperatura de precalentamiento para controlar de manera proactiva las transformaciones metalúrgicas en el interior de la Zona Afectada por el Calor (Heat Affected Zone, HAZ). Dado que el coste medio de una reparación o de una sustitución de un tramo corto de raíl puede ser del orden de miles de euros y que la frecuencia de defectos en la conexión entre raíl y rueda aumentará previsiblemente con el evidente incremento en los niveles de tráfico en la mayoría de líneas de ferrocarril, resulta sencillo comprender la importancia del nuevo proceso.
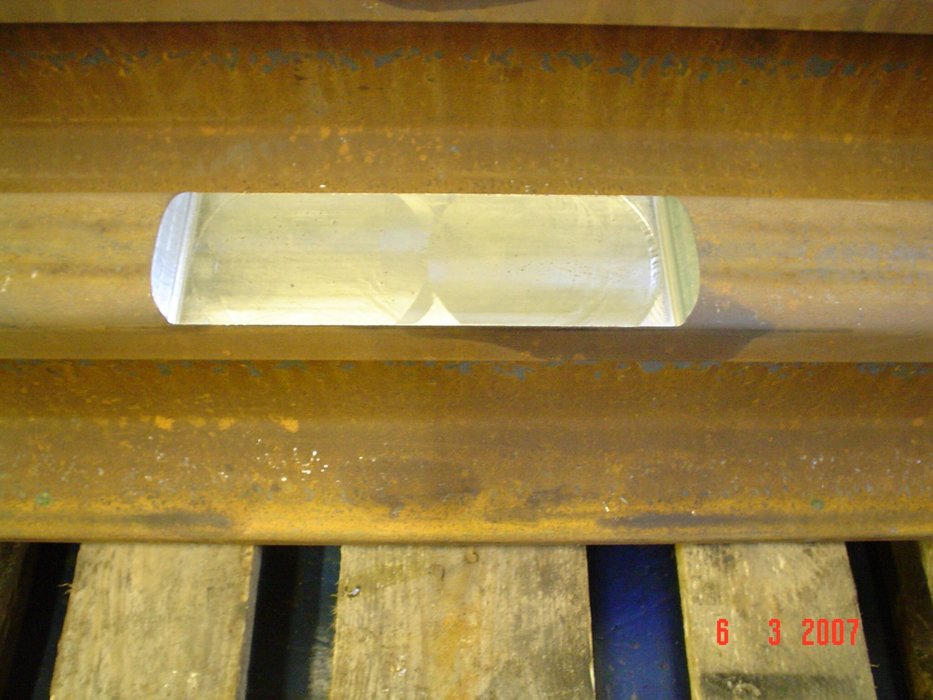
El proceso ha sido sometido a un riguroso conjunto de pruebas y actualmente se está fabricando una unidad dedicada para realizar la demostración sobre la propia vía en varias redes europeas, entre ellas en Francia y el Reino Unido.
El rodaje de las ruedas de los coches sobre los raíles genera unos patrones de esfuerzo de elevada magnitud y complejidad para el contacto entre raíl y rueda, lo que provoca la degradación de la superficie. La amplia variedad de diseños de la vía, perfiles de rueda y tipo de tráfico pueden dar como resultado una amplia variedad de defectos en la superficie que reduce la vida operativa del raíl. Se producen defectos como deformaciones y erosiones de las ruedas incluso en las redes ferroviarias más modernas y con un buen mantenimiento y, por regla general, cada red desarrolla uno de estos defectos al año y por cada dos kilómetros. La sustitución de estos defectos con una sección corta de raíl resulta cara y no siempre es deseable dado que introduce dos nuevas discontinuidades en la vía en forma de dos soldaduras aluminotérmicas (reacción exotérmica que utiliza aluminio como agente reductor) que elimina las ventajas obtenidas con los raíles largos de instalación en caliente (hasta 120 metros). La técnica convencional alternativa para la reparación de estos defectos es el proceso de soldadura Manual por Arco Metálico (Manual Metal Arc, MMA). Aunque esta técnica se utiliza en numerosos sectores industriales, depende enormemente de la pericia del soldador, consume mucho tiempo y es proclive a sufrir defectos internos como la porosidad, que posteriormente se ve acentuada por la fatiga, y si no se detecta mediante inspección ultrasónica provoca rupturas del raíl.
Los siguientes factores hacen que el nuevo proceso desarrollado resulte económico y aporte robustez técnica:
1. El paso de la temperatura convencional de precalentamiento de 3500C a sólo 800C tiene la ventaja de una reparación más rápida, una profundidad reducida de la zona afectada por el calor y una microestructura más robusta.
2. La utilización de una eliminación estandarizada del área del defecto mediante un fresado controlado tiene la ventaja de su reproducibilidad y deja de lado la valoración subjetiva del operario.
3. La utilización de un proceso programado y semiautomático de soldadura por arco abierto con arco de núcleo fundente asegura el control del calor generado y de unos tiempos de trabajo predecibles.
La calidad de la superficie de rodadura restaurada por la soldadura gracias al proceso desarrollado queda garantizada pues la reparación es extremadamente resistente a la fatiga y presenta una resistencia al desgaste similar a la de un raíl estándar Grado R260 con uniformidad de dureza y microestructuras a lo largo del área restaurada por la soldadura.
La nueva técnica de reparación patentada por Tata Steel se realiza en cuatro pasos.
El defecto se elimina primero utilizando una fresadora portátil triaxial del raíl que se sujeta a ambos lados del raíl. Ello asegura una excavación correcta del defecto identificado. Esto supone por sí mismo una notable mejora respecto al rectificado manual o al escarpado con soplete, ninguno de los cuales proporciona una forma de la cavidad consistente o un acabado de la superficie que facilite la soldadura automática programada.
En segundo lugar, el área adyacente y la cavidad se precalientan con un mechero convencional. Para raíles de Grado 260, la temperatura aconsejada es de 60 a 80°C. La elección de esta temperatura es para el control de la microestructura en la Zona Afectada por el Calor y la forma de la textura cuadrada programada de la deposición de las perlas posteriores/adyacentes asegura que la microestructura en la HAZ sea perlita de calidad y sin martensita fragilizadora. Esta temperatura está indicada para la gran mayoría de aceros con alto contenido de carbono para raíles actualmente en uso pero podría ser necesario modificarla para aceros con unas características diferentes de transformación como aceros bainíticos con bajo contenido de carbono y sin carburo.
La tercera fase utiliza una máquina de reparación de soldadura semiautomática, con un proceso de soldadura de arco abierto, un consumible para soldadura TN3-0 aprobado por Network Rail (Reino Unido) y los parámetros de soldadura aconsejados. La colocación de la capa superior es crucial para evitar la formación de una nueva Zona Afectada por el Calor (Heat Affected Zone, HAZ). La mayor parte de la capa superior de soldadura se elimina parcialmente mediante rectificado del perfil.
El cuarto y último paso consiste en restaurar y mezclar el perfil del raíl transversal y longitudinal mediante rectificado, utilizando para ello rectificadoras de raíl convencionales.
Se obtuvo una evaluación comparativa entre la técnica MMA existente y el nuevo proceso mediante el registro del historial térmico de ambos procesos utilizando acoplamientos térmicos embebidos. Varias conclusiones fundamentales demuestran la robustez metalúrgica del proceso:
- Pese al calentamiento a sólo 80°C, la temperatura en la HAZ tras cada perla de soldadura depositada permanece por encima de 200°C, evitando así cualquier transformación a la microestructura martensítica (dado que la temperatura de inicio de la formación de martensita es de 160°C para raíles de grado 260).
- Las velocidades de enfriamiento en el proceso desarrollado son casi idénticas a las del proceso MMA convencional para todas las etapas de deposición excepto la primera. La velocidad más rápida de 5,2 °C/s tras la primera perla de soldadura también equivale a la mitad de la velocidad crítica para la transformación a martensita.
- Se aprecia una conexión de depósito de soldadura sin roturas con una microestructura completamente perlítica, sin martensita ni bainita.
- El perfil de dureza indica que la resistencia al desgaste del depósito bainítico de soldadura será comparable al de un raíl de grado R260 y asegura un buen perfil longitudinal.
- El depósito de soldadura fue sometido a una prueba de fatiga por plegado con un rango de esfuerzos aplicados equivalentes a tres veces el previsto una vez puesto en servicio. Se completaron con éxito cinco millones de ciclos sin fallos. El mismo depósito resistió con éxito otros 4,3 millones de ciclos con un rango de esfuerzos aplicados equivalentes a ocho veces el previsto una vez en servicio.
El rodaje de las ruedas de los coches sobre los raíles genera unos patrones de esfuerzo de elevada magnitud y complejidad para el contacto entre raíl y rueda, lo que provoca la degradación de la superficie. La amplia variedad de diseños de la vía, perfiles de rueda y tipo de tráfico pueden dar como resultado una amplia variedad de defectos en la superficie que reduce la vida operativa del raíl. Se producen defectos como deformaciones y erosiones de las ruedas incluso en las redes ferroviarias más modernas y con un buen mantenimiento y, por regla general, cada red desarrolla uno de estos defectos al año y por cada dos kilómetros. La sustitución de estos defectos con una sección corta de raíl resulta cara y no siempre es deseable dado que introduce dos nuevas discontinuidades en la vía en forma de dos soldaduras aluminotérmicas (reacción exotérmica que utiliza aluminio como agente reductor) que elimina las ventajas obtenidas con los raíles largos de instalación en caliente (hasta 120 metros). La técnica convencional alternativa para la reparación de estos defectos es el proceso de soldadura Manual por Arco Metálico (Manual Metal Arc, MMA). Aunque esta técnica se utiliza en numerosos sectores industriales, depende enormemente de la pericia del soldador, consume mucho tiempo y es proclive a sufrir defectos internos como la porosidad, que posteriormente se ve acentuada por la fatiga, y si no se detecta mediante inspección ultrasónica provoca rupturas del raíl.
Los siguientes factores hacen que el nuevo proceso desarrollado resulte económico y aporte robustez técnica:
1. El paso de la temperatura convencional de precalentamiento de 3500C a sólo 800C tiene la ventaja de una reparación más rápida, una profundidad reducida de la zona afectada por el calor y una microestructura más robusta.
2. La utilización de una eliminación estandarizada del área del defecto mediante un fresado controlado tiene la ventaja de su reproducibilidad y deja de lado la valoración subjetiva del operario.
3. La utilización de un proceso programado y semiautomático de soldadura por arco abierto con arco de núcleo fundente asegura el control del calor generado y de unos tiempos de trabajo predecibles.
La calidad de la superficie de rodadura restaurada por la soldadura gracias al proceso desarrollado queda garantizada pues la reparación es extremadamente resistente a la fatiga y presenta una resistencia al desgaste similar a la de un raíl estándar Grado R260 con uniformidad de dureza y microestructuras a lo largo del área restaurada por la soldadura.
La nueva técnica de reparación patentada por Tata Steel se realiza en cuatro pasos.
El defecto se elimina primero utilizando una fresadora portátil triaxial del raíl que se sujeta a ambos lados del raíl. Ello asegura una excavación correcta del defecto identificado. Esto supone por sí mismo una notable mejora respecto al rectificado manual o al escarpado con soplete, ninguno de los cuales proporciona una forma de la cavidad consistente o un acabado de la superficie que facilite la soldadura automática programada.
En segundo lugar, el área adyacente y la cavidad se precalientan con un mechero convencional. Para raíles de Grado 260, la temperatura aconsejada es de 60 a 80°C. La elección de esta temperatura es para el control de la microestructura en la Zona Afectada por el Calor y la forma de la textura cuadrada programada de la deposición de las perlas posteriores/adyacentes asegura que la microestructura en la HAZ sea perlita de calidad y sin martensita fragilizadora. Esta temperatura está indicada para la gran mayoría de aceros con alto contenido de carbono para raíles actualmente en uso pero podría ser necesario modificarla para aceros con unas características diferentes de transformación como aceros bainíticos con bajo contenido de carbono y sin carburo.
La tercera fase utiliza una máquina de reparación de soldadura semiautomática, con un proceso de soldadura de arco abierto, un consumible para soldadura TN3-0 aprobado por Network Rail (Reino Unido) y los parámetros de soldadura aconsejados. La colocación de la capa superior es crucial para evitar la formación de una nueva Zona Afectada por el Calor (Heat Affected Zone, HAZ). La mayor parte de la capa superior de soldadura se elimina parcialmente mediante rectificado del perfil.
El cuarto y último paso consiste en restaurar y mezclar el perfil del raíl transversal y longitudinal mediante rectificado, utilizando para ello rectificadoras de raíl convencionales.
Se obtuvo una evaluación comparativa entre la técnica MMA existente y el nuevo proceso mediante el registro del historial térmico de ambos procesos utilizando acoplamientos térmicos embebidos. Varias conclusiones fundamentales demuestran la robustez metalúrgica del proceso:
- Pese al calentamiento a sólo 80°C, la temperatura en la HAZ tras cada perla de soldadura depositada permanece por encima de 200°C, evitando así cualquier transformación a la microestructura martensítica (dado que la temperatura de inicio de la formación de martensita es de 160°C para raíles de grado 260).
- Las velocidades de enfriamiento en el proceso desarrollado son casi idénticas a las del proceso MMA convencional para todas las etapas de deposición excepto la primera. La velocidad más rápida de 5,2 °C/s tras la primera perla de soldadura también equivale a la mitad de la velocidad crítica para la transformación a martensita.
- Se aprecia una conexión de depósito de soldadura sin roturas con una microestructura completamente perlítica, sin martensita ni bainita.
- El perfil de dureza indica que la resistencia al desgaste del depósito bainítico de soldadura será comparable al de un raíl de grado R260 y asegura un buen perfil longitudinal.
- El depósito de soldadura fue sometido a una prueba de fatiga por plegado con un rango de esfuerzos aplicados equivalentes a tres veces el previsto una vez puesto en servicio. Se completaron con éxito cinco millones de ciclos sin fallos. El mismo depósito resistió con éxito otros 4,3 millones de ciclos con un rango de esfuerzos aplicados equivalentes a ocho veces el previsto una vez en servicio.