www.revista-fabricacion.com
18
'17
Written on Modified on
Enfoque práctico para el control de material desechado en la fabricación
Los fabricantes buscan constantemente formas de maximizar la productividad y la eficiencia. Actualmente, esos esfuerzos a menudo implican programas de alto nivel que emplean términos de moda como sistemas informáticos en la nube, fabricación asistida por datos, sistemas ciberfísicos e Industria 4.0. Estas iniciativas de última generación son grandes conceptos y pueden producir resultados impresionantes. Sin embargo, la realidad del mundo de la fabricación interfiere normalmente en la implementación de esos planes tan ambiciosos, y una realidad crucial es la presencia de material desechado incontrolado en el proceso de fabricación. Por tanto, antes de hablar de digitalización y optimización, es necesario que el fabricante examine sus operaciones, determine dónde se producen desperdicios y desarrolle métodos para reducirlos o eliminarlos. Controlar el material desechado es el primer paso de una empresa de fabricación de cara a prepararse para la adopción de sofisticadas estrategias de fabricación inteligentes. Figura 1: imagen completa de todos los elementos y cómo se relacionan e interactúan en una planta de fabricación (modelo y concepto de NEXT STEP).
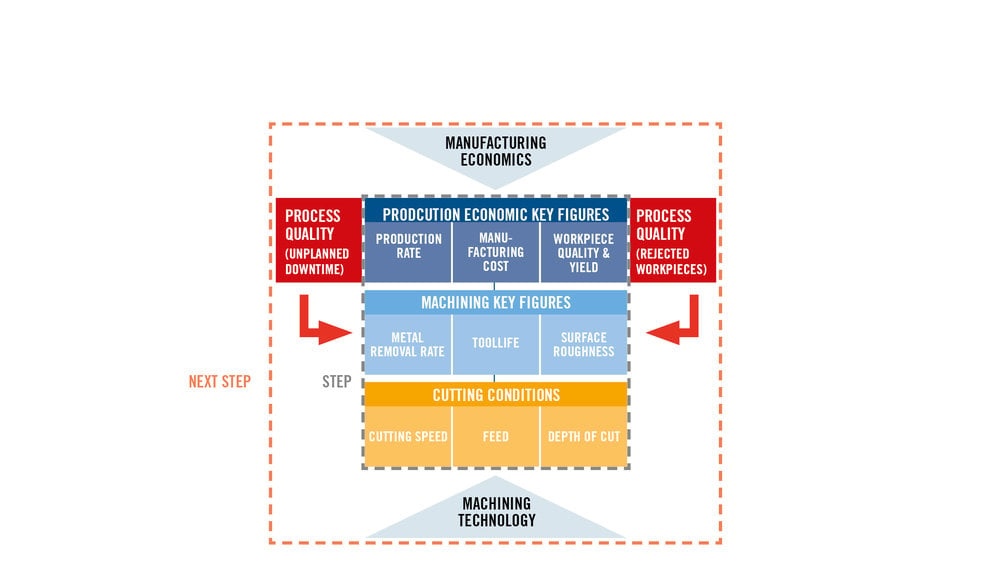

Conceptos básicos de la economía en la producción
La fabricación se compone de una serie de procesos de transformación. Un taller transforma materia prima en piezas terminadas o semiacabadas a través de una serie de operaciones de transformación individuales como la fundición, la soldadura o el mecanizado. Además, cada operación está comprendida por una serie de elementos individuales. Así, los elementos básicos del mecanizado, por ejemplo, incluyen la herramienta de corte, la máquina-herramienta, los accesorios y el suministro de refrigerante. Todos estos elementos juntos constituyen un sistema de mecanizado que recibe el apoyo de los equipos y componentes relacionados en un sistema de producción.
Cabe mencionar que la planificación, la programación y la gestión económica funcionan en relación al sistema de producción para crear un entorno de producción. Sin embargo, el elemento clave de un entorno de producción son las personas. Aunque en el sector de la fabricación actual se utiliza un gran número de ordenadores, robots y otras tecnologías avanzadas, las personas siguen siendo las que toman las decisiones que controlan todo ese entorno.
En cuanto al proceso de mecanizado, este se basa en los datos de aplicaciones técnicas relacionados con la selección de herramientas, las condiciones de corte, la programación, y el material y sujeción de piezas. Otros detalles clave incluyen los requisitos del volumen de producción y la calidad específica de las piezas acabadas.
La vinculación de estos datos de aplicaciones técnicas con las repercusiones económicas es conocida como la economía en la producción. El objetivo de la ciencia de la economía en la producción es conseguir un equilibrio entre todos los factores que intervienen. Mientras que los elementos técnicos producen los resultados deseados en términos de calidad de la pieza, la cantidad y la puntualidad, las operaciones deben llevarse a cabo a un coste que permita a prosperar a una empresa.
Así pues, el equilibrio entre la producción y los costes de mecanizado se desarrolla en tres fases. La primera fase consiste en el establecimiento de un proceso de mecanizado fiable que es esencial para minimizar incidencias inesperadas como la ruptura de herramientas, virutas incontroladas y piezas destruidas. Un taller fija su estándar de fiabilidad operativa mediante la elección de herramientas con una capacidad de carga que cumpla o supere la capacidad de las cargas mecánicas, térmicas, químicas y tribológicas generadas en el proceso de mecanizado.
Figura 2: modelo de maquinabilidad total desarrollado en STEP.
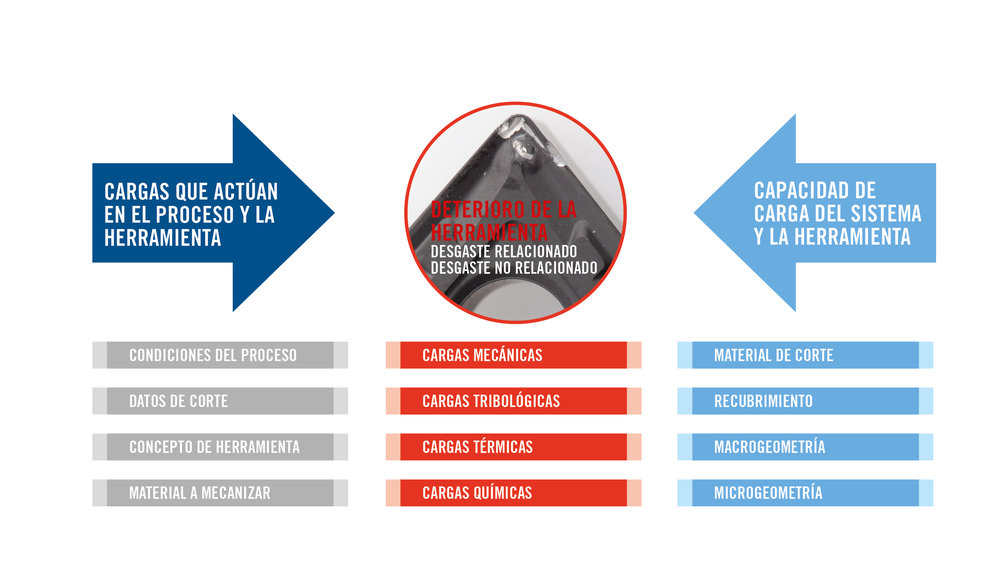
HQ_ILL_Machinability _model
La segunda fase para conseguir una economía en la producción equilibrada implica la elección de unas condiciones de corte que reflejen las limitaciones del proceso de mecanizado impuestas por las circunstancias reales. Las capacidades teóricas de una herramienta de corte pueden ser muy amplias, pero la realidad concreta de cada taller restringe el rango de parámetros de aplicación eficaces.
Por ejemplo, las capacidades y el rendimiento de una herramienta varían según la cantidad de potencia de la máquina-herramienta que la vaya a aplicar; las características de mecanizado del material de la pieza o la configuración de una pieza que pueda ser propensa a las vibraciones o distorsiones. Aunque existe una amplia selección de condiciones de corte que en teoría funcionarían, lamentablemente las limitaciones que impone la realidad reducen la gama de posibles elementos aptos y que no presentarían problemas.
La Figura 3 muestra una amplia selección o volumen de velocidades de corte, profundidades de corte y avances que se han reducido a una selección más pequeña y a un volumen reducido tras reconocer las diferentes realidades de una determinada aplicación de corte.
Figura 3: ilustración en 3D que muestra la recopilación de todas las combinaciones de condiciones de corte que pueden utilizarse con las limitaciones del entorno de corte.
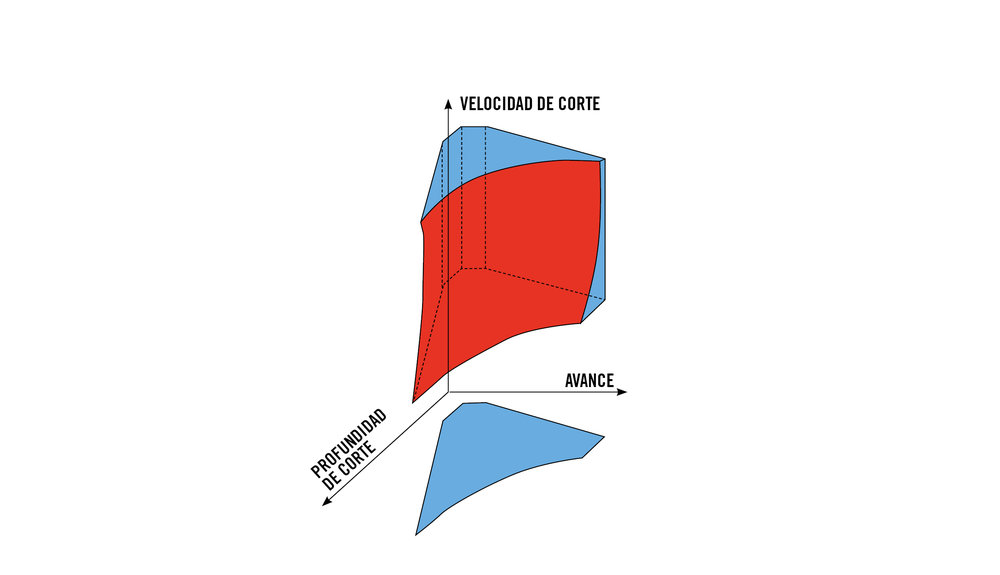
HQ_ILL_Machining_Process_cutting_conditions
Si se aplican condiciones de corte sin tener en cuenta las limitaciones de aplicación de una situación específica, habrá consecuencias económicas negativas, como mayores costes y menor productividad. Tal vez, el 90 % de los problemas experimentados durante el mecanizado surgen porque no se respetan las limitaciones que la realidad de un taller impone en el proceso de corte.
En cambio, si las condiciones de corte no exceden las limitaciones impuestas por las realidades del taller, la operación es segura desde una perspectiva técnica. Sin embargo, no todas las combinaciones de condiciones de corte técnicamente seguras resultan igual de rentables. Si se usan unas condiciones de corte más agresivas pero técnicamente seguras, aumentará la producción de piezas acabadas, pero después de cierto punto la productividad disminuirá porque el uso de parámetros de corte agresivos reduce la vida útil de la herramienta. De esta forma, es cuestión de tiempo que la producción de piezas también se reduzca ya que se pasará más tiempo cambiando herramientas desgastadas.
En algún lugar existe una combinación de condiciones de corte que ofrezca un equilibrio entre el rendimiento productivo y el coste de fabricación. La figura 4 muestra la relación entre las condiciones de corte, la productividad y los costes de la máquina y las herramientas. (En el gráfico se presentan solo los elementos que varían a medida que cambian las condiciones de corte: el material, los costes generales, de ingeniería y administración no están incluidos). Las condiciones más agresivas están en el lado derecho de los ejes, y la mayor productividad en la parte superior. La zona azul pálido del centro del gráfico indica que las condiciones de corte generan una mezcla equilibrada de productividad (mayor producción) y rentabilidad (menor coste).
Figura 4: relación entre las condiciones de corte, la productividad y los costes de mecanizado. Esta figura muestra un modelo simplificado, sin tener en cuenta los factores de material desechado.
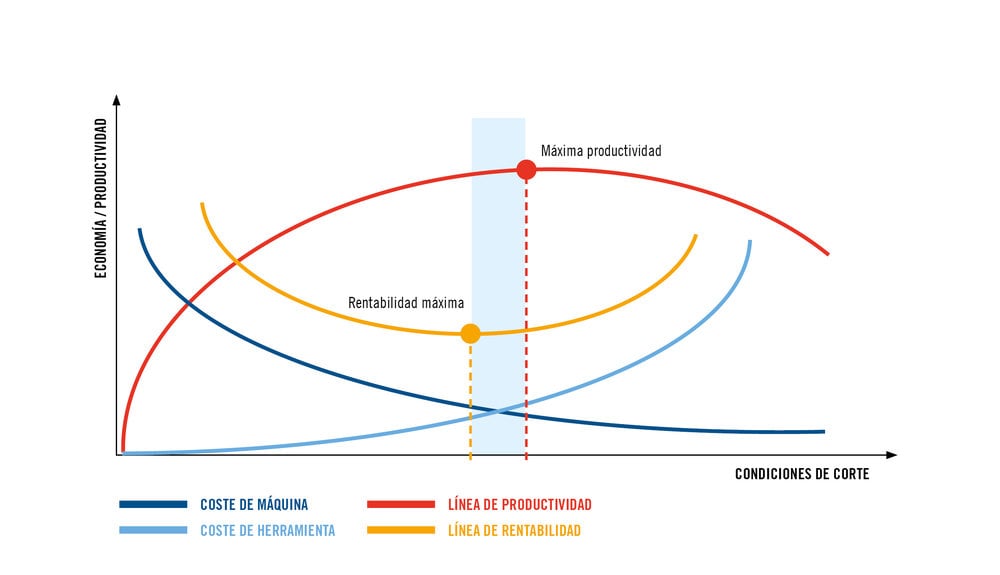
HQ_ILL_Machining_Process_relationship_cutting_conditions_productivity_machining_costs
Como consecuencia, la tercera fase para conseguir una economía en la producción equilibrada implica determinar la combinación óptima de las condiciones de corte para una situación dada. Es fundamental tener en cuenta todos los factores de la operación de mecanizado para establecer un dominio de trabajo en el que los parámetros de corte proporcionen los niveles de productividad y rentabilidad deseados.
El efecto económico del material de desecho en la producción
Lamentablemente, los elegantes métodos científicos para disponer de un rendimiento económico equilibrado en la producción funcionan a merced del material de desecho del sistema de fabricación. El material de desecho destruye el equilibrio, y estos surgen de muchas maneras. Por ejemplo, es un desperdicio de energía y potencia cuando se usa una máquina-herramienta de 60 kW en una aplicación en curso que solo requiere 15 kW. Otra situación similar es cuando las piezas terminadas no cumplen los niveles de calidad necesarios; en este caso se malgasta el tiempo, el dinero y los recursos invertidos en este proceso para acabar obteniendo un resultado inaceptable. Asimismo, la fabricación de las piezas que superan innecesariamente los niveles de calidad supone también un malgasto, ya que lograr una mayor calidad aumenta los costes.
Una situación menos evidente y menos entendida es la infrautilización o uso indebido de los recursos intelectuales. Algunos empleados de una empresa pueden poseer conocimientos o aptitudes que ayudarían a la empresa a conseguir sus objetivos, pero por motivos como una comunicación deficiente o por políticas internas de la empresa, los conocimientos y aptitudes no se comparten y, por lo tanto, se genera un desperdicio.
Herramientas de reducción del material de desecho
Tras identificar y clasificar el material de desecho, un taller debería crear un plan para reducirlo o eliminarlo. Existe una amplia gama de herramientas que permiten a un fabricante identificar, cuantificar y minimizar las prácticas que producen desperdicios. Por ejemplo, el análisis del uso, la manipulación y el deterioro de la herramienta señala las áreas con problemas.
Tales análisis han demostrado que, en algunos casos, hasta un 20 % o 30 % de las herramientas que el personal define como desgastadas, de hecho todavía podían usarse, por lo que se acaba desaprovechando la vida útil restante de la herramienta. El establecimiento claro de criterios de desgaste y la comunicación de las normas al personal del taller reduce significativamente el desperdicio de vida útil de las herramientas.
Asimismo, los análisis de los tiempos muertos de la máquina cuantifican el tiempo empleado en actividades como la configuración, la programación y el cambio de herramientas. Estos análisis indican a menudo que del 50 % al 60 % de los tiempos muertos de la máquina se podrían evitar mediante una mejor comprensión, ejecución y coordinación de estas actividades tan necesarias como laboriosas.
Gracias al uso de las entrevistas, encuestas y programas de formación, se puede sacar a relucir una gran cantidad de información útil al tratar cuestiones del personal en las que se hablen del desperdicio de los recursos intelectuales, así como de conocimientos y aptitudes aún desconocidos. Como resultado, los empleados realizan mejor su trabajo y se fomentan aptitudes para maximizar la productividad del personal.
Gestión de actividades que aportan valor, actividades que aumentan el valor y actividades innecesarias
A principios del siglo XX, el ingeniero industrial americano Fredrick Taylor estudió las operaciones de taller y propuso que la mejora de la productividad fuera impulsada por la eliminación de todas las actividades del proceso que no aportaran valor al producto final. Las directrices de la moderna "producción ajustada" siguen esta misma línea de pensamiento.
En las operaciones de mecanizado, las únicas actividades que verdaderamente añaden valor son en realidad el mecanizado y la generación de virutas. Otras acciones como la carga de piezas y la sujeción, se consideran actividades que permiten añadir valor, pero que no añaden valor directamente al producto fabricado, si bien son necesarias para las actividades que aportan valor.
Un tercer grupo de actividades del sistema de mecanizado son las innecesarias. Estas actividades ni crean valor ni permiten la creación de valor, sino que consumen recursos sin aportar ningún beneficio. Simplemente son un desperdicio. La solución de problemas es un ejemplo de actividad innecesaria. Si un proceso está diseñado correctamente y se controla desde el primer momento, no habrá problemas y no se perderá tiempo en resolverlos.
Figura 5: imagen esquemática de un taller de mecanizado y todos los elementos relacionados con el mismo.
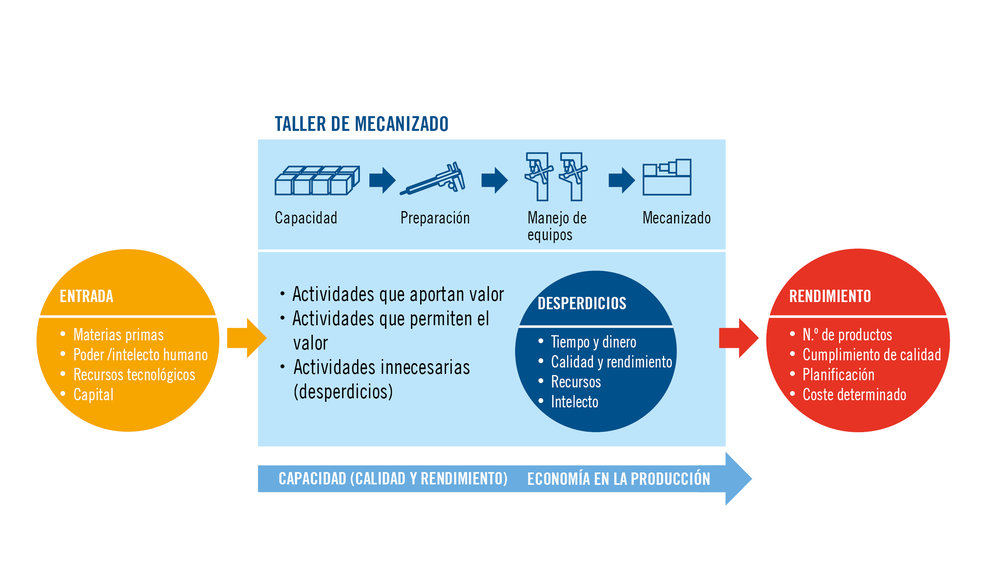
HQ_ILL_Machining_process_workshop
Conclusión
Durante mucho tiempo, las actividades innecesarias se han aceptado como parte del proceso de fabricación y no se han reconocido como notables factores de perturbación a la hora de conseguir una economía de producción equilibrada. Actualmente, se está prestando mucha atención a eliminar o reducir al mínimo las actividades innecesarias. El objetivo de la planificación de capacidades y productividad es eliminar las actividades innecesarias, minimizar las actividades que permiten el valor y optimizar las actividades que aportan valor. (Consulte la figura 6).
Figura 6: presentación de actividades que aportan valor (naranja), actividades que permiten el valor (azul) y actividades de material de desecho (rojo). El factor humano (gris) es el elemento clave para alcanzar la optimización máxima de un rendimiento de fabricación superior.
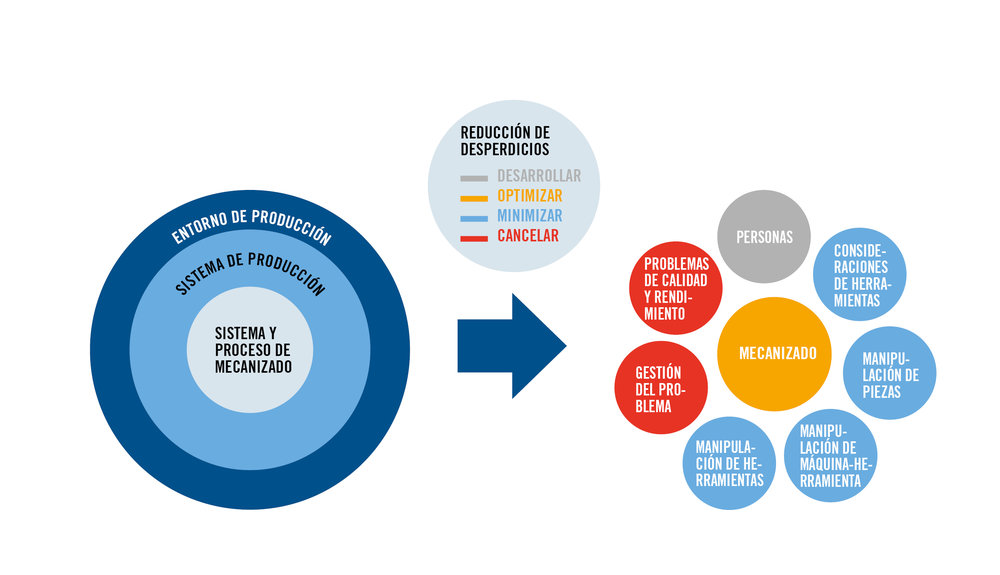
HQ_ILL_Machining_system_process
Cuando se elimina el material de desecho, la teoría de la economía en la producción se convierte en práctica. En este punto, el progreso de la economía en la producción puede aplicarse directamente al éxito de la empresa. Sin embargo, en el esfuerzo por eliminar todas las formas de desperdicio, es primordial ser cautelosos. Es importante calcular la rentabilidad de la inversión de las actividades de reducción de desperdicios. La eliminación total de cierta incidencia de desperdicios podría implicar una inversión tan grande que, desde una perspectiva económica, podría ser mejor aceptar los desperdicios (o parte de ellos) y seguir viviendo con ellos. Tales decisiones se toman después de realizar los análisis cuantitativos adecuados, así como los debates empresariales internos acerca de cómo las decisiones pueden afectar a los objetivos y a la filosofía de la empresa.
Notas:
Servicios de consultoría de Seco
A medida que los productos elaborados son cada vez más sofisticados, los usuarios necesitan una mayor asistencia para las aplicaciones y poder darse cuenta de cómo obtener el máximo beneficio de las nuevas tecnologías. En el mecanizado, el nivel de asistencia inicial consiste en una orientación en la selección de la herramienta correcta para una determinada operación. Tras seleccionar una herramienta, poder contar con más información facilita la elección de las condiciones de corte óptimas, el uso de refrigerante y otras consideraciones. Entonces, si una herramienta no funciona como se espera en dicha operación, el proveedor puede proporcionar ayuda para solucionar los problemas. Estos tres modos de asistencia constituyen los servicios tradicionales relacionados con las herramientas.
Cuando el servicio de herramientas se amplía de la simple aplicación a cubrir un proceso en el que la pieza está sujeta a varias operaciones en una o más máquinas, los usuarios finales necesitan formación para organizar la secuencia de operaciones, la manipulación de la pieza y otros factores para maximizar la eficiencia y la productividad. Ese nivel de asistencia puede denominarse servicios de ingeniería.
Cada vez con mayor frecuencia, los fabricantes buscan asesoramiento para mejorar las funciones, la producción y el control de costes para un taller o toda la organización. En estos casos, algunas empresas de consultoría independientes realizan lo que se describiría como consultas de gestión o producción. Sin embargo, para llevar a cabo una verdadera evaluación de una organización de producción, es fundamental comprender al cien por cien las operaciones principales de dicha empresa.
Gracias a sus años de experiencia y su excepcional conocimiento de las herramientas y los procesos de mecanizado, Seco viene proporcionando servicios de herramientas tradicionales, servicios de ingeniería y en cierta medida servicios de consultoría más amplios durante las últimas décadas. Estos servicios se han ofrecido en situaciones de contingencia o circunstancias muy específicas, pero en 2016, Seco fundó sus Servicios de consultoría para ofrecer a sus clientes un abanico más dinámico y optimizado de servicios de producción.
Los Servicios de consultoría de Seco incluyen una amplia gama de recursos específicos y métodos de entrega. La selección de herramientas y la asistencia en aplicaciones está disponible online de forma ininterrumpida para satisfacer las necesidades de productividad inmediatas de los talleres.
Los servicios de ingeniería pueden comenzar con comunicaciones electrónicas y ampliarse a visitas in situ llagado el caso. Los Servicios de consultoría de Seco también pueden incluir un análisis exhaustivo y asesoramiento sobre el funcionamiento de cada función en el taller. Estos servicios pueden incluir consultas sobre el mantenimiento de la máquina-herramienta, disposición del taller, logística y funciones organizativas. Además, también se pueden incluir asesoramiento sobre problemas de conocimientos del personal y sus aptitudes, la relación de las técnicas de fabricación empleadas en las estrategias de producción de la organización, así como repercusiones de costes.
Cada relación de consultoría de Seco se basa en el concepto NEXT STEP, pero también se adapta a las necesidades específicas de la organización participante, y se desarrolla como un diálogo entre Seco y el cliente dirigido a conseguir un objetivo común.