www.revista-fabricacion.com
05
'20
Written on Modified on
Fabricación aditiva: liberar el potencial disruptivo
La creciente popularidad de la impresión 3D, también llamada fabricación aditiva, constituye un buen presagio para el futuro sostenible de nuestro planeta.
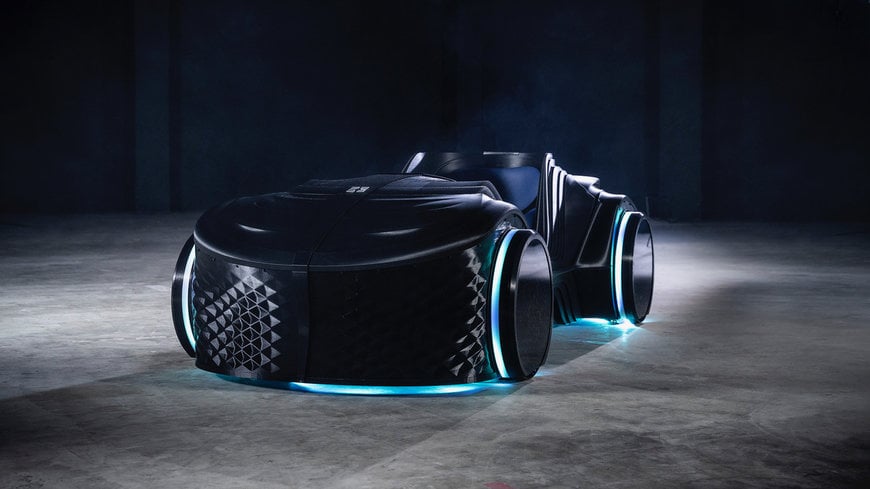
La impresión 3D o fabricación aditiva ha sido descrita como una de las tecnologías más disruptivas de la era moderna y es la clave para el futuro de la industria. Se inventó a principios de los años 80 y su aceptación ha aumentado enormemente en los últimos años gracias a la rápida evolución y a la convergencia de diversas tecnologías en la era digital que han facilitado su acceso a profesionales y aficionados.
La fabricación aditiva (AM, por sus siglas en inglés) o impresión 3D antes se empleaba en exclusiva con el fin de obtener prototipos rápidos y ahora es la respuesta para fabricar productos o piezas, en cualquier sitio y a cualquier hora. La fabricación convencional o sustractiva recurre a procesos como el fresado, el torneado o el desbastado para retirar material, mientras que la AM añade material capa a capa para crear un objeto o una pieza mediante software CAD o un escaneado en 3D de un objeto. En la AM se utilizan muchos procesos, tecnologías y materiales diferentes, y la gama de estos últimos va desde los termoplásticos hasta los metales y también desde la cerámica hasta los bioquímicos que se utilizan frecuentemente en implantes médicos.
Una de las principales ventajas de la fabricación aditiva es que permite la producción de piezas personalizadas bajo demanda a un precio relativamente asequible; estas piezas van desde una rueda perdida de un coche de juguete hasta las ruedas oruga del vehículo Mars Rover. También es de destacar que este proceso también permite aplicar diseños complicados con geometrías complejas que reducen peso y añaden resistencia a piezas difíciles y/o caras de fabricar con métodos tradicionales.
El ejemplo del inyector de combustible diseñado e impreso en 3D por GE para el motor a reacción LEAP es muy conocido: este complejo inyector del tamaño de una nuez constaba antes de 20 piezas ensambladas y ahora es una maravilla de ingeniería de una sola pieza gracias a la impresión 3D. Además, pesa un 25% menos que su equivalente fabricado de manera tradicional, dura cinco veces más y es un 30% más rentable.
Janne Kyttanen es un visionario 3D e inventor de 3DTI, la primera tecnología de fabricación que incorpora la impresión 3D a la personalización masiva. Jane afirma que la única limitación de las aplicaciones de AM es la creatividad. Las ventajas de la fabricación AM son numerosas pero también hay inconvenientes, el más importante de los cuales es el elevado coste de las inversiones iniciales, así como los gastos operativos. Estos últimos se deben al elevado coste de los materiales que en la mayoría de los casos los suministran los fabricantes del hardware, y están atados por acuerdos OEM. Esto también excluye a la fabricación en serie, sobre todo de grandes piezas, ya que la economía aquí se decanta claramente por los procesos de fabricación convencionales.
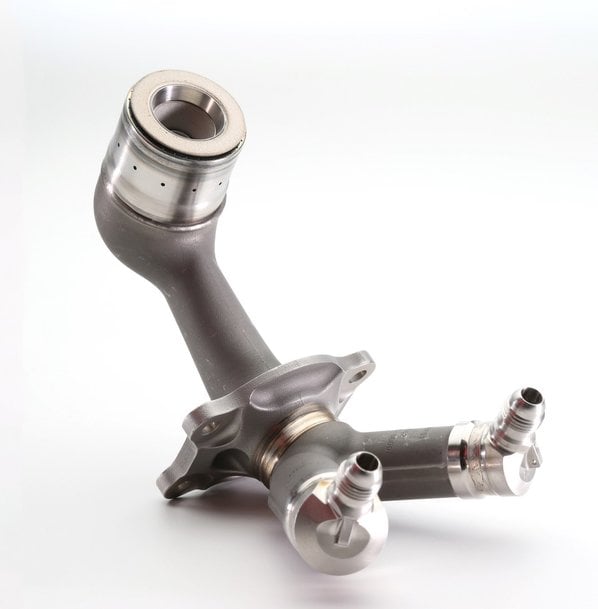
Inyector de combustible diseñado por GE para el motor a reacción LEAP
Sin embargo, la AM ofrece grandes ventajas sin que importe en tamaño ni los volúmenes cuando se trata de requisitos especiales. El ejemplo es el soporte del asiento, una pieza estándar en el automóvil que asegura los cierres del cinturón de seguridad a los asientos y los asientos al suelo del vehículo, fabricado en General Motors con el software de diseño generativo Autodesk. Lo que antes era un componente cuadrado y formado por ocho piezas soldadas ahora es un anclaje elegante de acero inoxidable impreso en 3D. El sustituto es ahora un 40% más ligero, un 20% más resistente y más barato de fabricar ya que reduce el número de proveedores y el trabajo de soldadura. No es extraño, pues, que todos los fabricantes de automóviles actuales hayan invertido en instalaciones AM en busca de la optimización del diseño del vehículo para ahorrar costes. Un coche típico tiene unas 30 000 piezas. Aunque no todas pueden fabricarse con impresión 3D hay muchas que sí se pueden fabricar así, como el soporte de asiento del ejemplo indicado antes, y aprovechan la evolución de la tecnología.
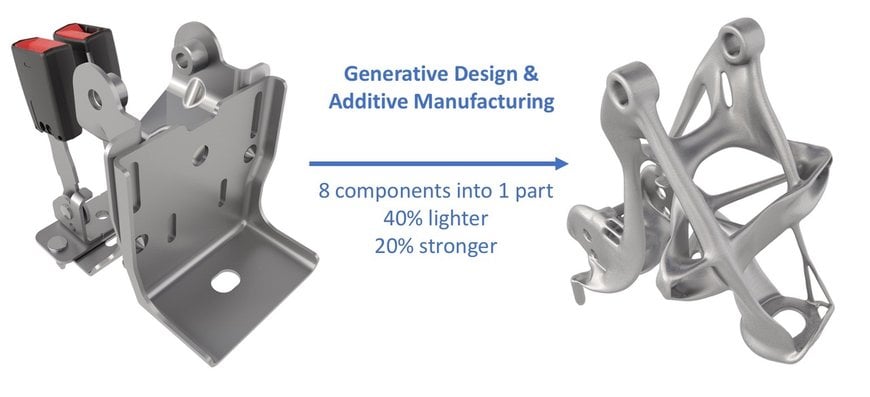
Soporte de asiento fabricado por General Motors
Innovaciones en Formnext
En Formnext 2019, la mayor feria europea dedicada a AM y a la siguiente generación de soluciones de fabricación inteligente, se dieron cita las principales compañías del sector, como 3D Systems, Addup, BigRep, DMG Mori, EOS, Formlabs, GE Additive, HP, Markforged, Renishaw, Siemens, Stratasys y Voxeljet, entre otras. Estas empresas presentaron muchas tecnologías de fabricación nuevas y más eficientes, así como soluciones avanzadas para usos industriales (software, hardware, materiales y servicios) además de un sinfín de anuncios de acuerdos y alianzas.
GE Additive, perteneciente a GE y líder mundial y pionera en tecnología aditiva, presentó un montón de productos incluida la Arcam EBM Spectra L, una impresora 3D de metal que cubre la mayor demanda procedente de la industria aeroespacial. Este nuevo modelo ofrece un mayor volumen de producción y más velocidad, una arquitectura integrada del sistema, análisis de estado de la máquina y opciones de automatización. La Spectra L ha sido desarrollada para aumentar la productividad y reducir el coste por pieza en un 10%, gracias a casi el doble de volumen de fabricación de la Arcan EBM Spectra H. La potencia del haz de 4,5 kW incrementa la velocidad de fabricación en un 20% si se compara con la Arcam EBM Q20plus.
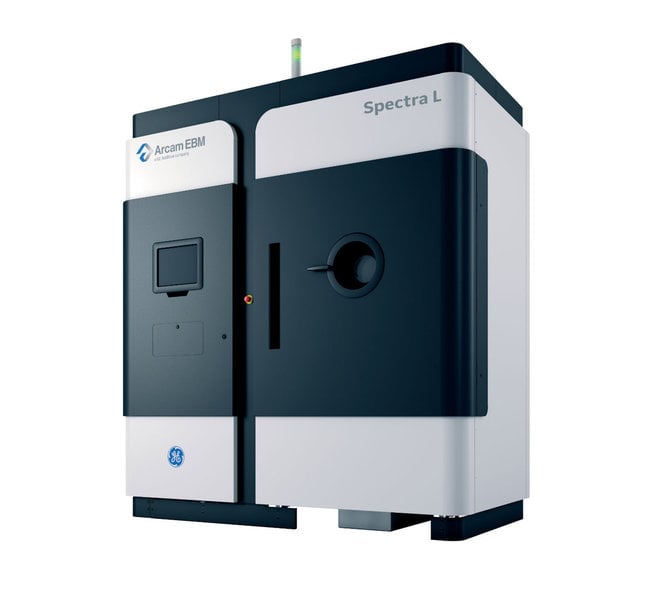
La compañía también presentó la impresora de metal Concept Laser M2 Series 5 que satisface las grandes expectativas de calidad y consistencia de pieza que los clientes esperan sobre todo en las altamente reguladas industrias aeroespacial y médica, que junto con la de automoción son los tres usuarios líderes de tecnologías AM.
BigRep, principal fabricante mundial de impresoras 3D, presentó un concepto de sistema automatizado de transporte (podcar) autónomo eléctrico impreso íntegramente en 3D, el LOCI. El prototipo LOCI está diseñado concretamente como "solución de transporte de corto alcance" para el entorno urbano, bien sea en aeropuertos y estaciones de tren, para el desplazamiento diario al trabajo y como transporte en el campus universitario y de reparto. El LOCI se desarrolló con modelado paramétrico y utiliza todo el potencial de la AM y su flexibilidad limitada. El diseño del podcar se puede personalizar fácilmente para un determinado lugar o una determinada aplicación. Se adapta el objetivo de transporte, los materiales, las propiedades estructurales, las ruedas especiales para diferentes terrenos, la marca personalizada y la energía solar integrada.
En Formnext la compañía presentó tres versiones diferentes del LOCI: el modelo Berlin LOCI presentado como un medio de transporte en el campus universitario unipersonal; el modelo San Francisco LOCI con carrocería estrecha para el transporte urbano; y el Dubai LOCI para el transporte aeroportuario con un aspecto lujoso exclusivo, paneles solares, espacio destinado al equipaje y ruedas robustas para clima desértico.
BigRep también dio a conocer el NEXT AGV, un vehículo autónomo guiado desarrollado junto con Bosch Rexroth y destinado a la zona de producción de la fábrica inteligente. El NEXT AGV impreso en 3D lleva implícita su producción ágil e inteligente y está impulsado por una unidad de energía inductiva que se alimenta de la red y se puede emplear como transporte logístico automatizado con una capacidad de carga de hasta 250 kg. En su plataforma se pueden montar herramientas y dispositivos adicionales como robots. Las ruedas especiales impresas en 3D de dos materiales diferentes permiten a la plataforma realizar movimientos laterales.
3D Systems, compañía cofundada en 1983 por Chuck Hull, el inventor de la impresión en 3D, mostró en Formnext 2019 cuatro soluciones de producción diseñadas concretamente para las industrias sanitaria, aeroespacial y de automoción. La compañía disfruta de una posición exclusiva para ofrecer soluciones concretas que cubran las necesidades de los clientes mediante servicios de hardware, software, materiales y profesionales que integran la producción aditiva en entornos de producción tradicionales. Gracias a una alianza estratégica con GF Machining Solutions, 3D Systems combina su innovación y experiencia en la fabricación aditiva con el liderazgo de 3D Machining Solutions en la mecanización de precisión. Esto permite a los fabricantes combinar de forma impecable las tecnologías aditiva y sustractiva para fabricar de manera más eficiente piezas complejas de metal con tolerancias precisas y reducir el coste total de la operación.
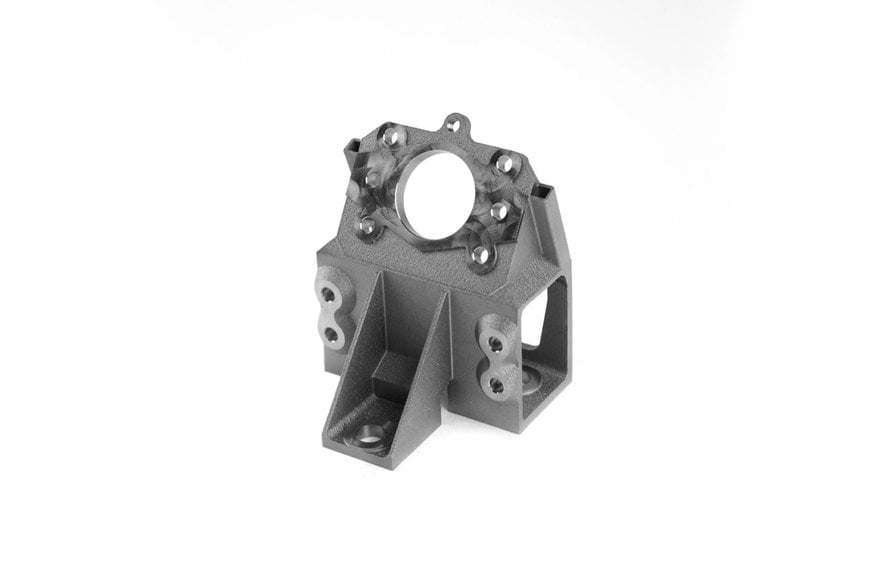
Soporte aeroespacial híbrido desarrollado por 3D Systems
Una de las soluciones presentadas en el stand conjunto fue el proceso de fabricación para crear un soporte aeroespacial en siete pasos que integra tecnologías aditivas, tecnologías tradicionales de metal y soluciones de software innovadoras con el fin de obtener piezas de alta calidad y repetibles a un precio optimizado por unidad.
EOS es un líder mundial en la tecnología de impresión 3D industrial de metales y polímeros que presentó por primera vez su tecnología Fine Detail Resolution (FDR) para el procesado de polímeros. EOS es el primer fabricante que desarrolla una solución para la impresión en 3D industrial basada en polvo utilizando un láser de CO. Esto permite fabricar piezas robustas y a la vez extremadamente delicadas con superficies de resolución muy alta y un grosor mínimo de la pared de solo 0,22 mm. Esto facilitará la implementación de nuevas aplicaciones para la producción en serie y ofrecerá una variedad aún mayor a la industria para elegir la tecnología de impresión 3D correcta de EOS destinada al procesamiento de polímeros.
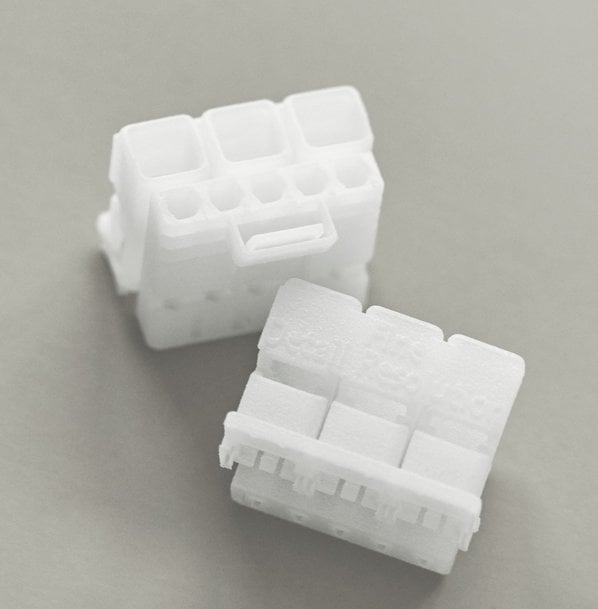
Enchufes impresos en 3D con tecnología FDR de EOS
La tecnología FDR combina lo mejor de dos mundos: la resolución detallada de la estereolitografía (SLA) con la duración y calidad del sinterizado selectivo por láser (SLS). Esta tecnología se presentó por primera vez en Formnext y abre posibilidades completamente nuevas de aplicación en el campo de la fabricación aditiva basada en polímero, por ejemplo, para unidades de filtro y canales de fluido, enchufes y otros componentes electrónicos, además de artículos de consumo como gafas.
Essentium, Inc. anunció la ampliación de su plataforma AM con la incorporación de materiales de alta temperatura (HT) y nuevos modelos de su galardonada plataforma de impresión Essentium High Speed Extrusion (HSE). La temperatura de la boquilla de la nueva HSE 180•S HT alcanza los 550 ºC y utiliza una amplia variedad de materiales para fabricar piezas que pueden resistir temperaturas de 180 ºC. Al comercializar una solución que ofrece las características de AM a alta temperatura sin comprometer velocidad, resistencia, escala o economía, Essentium ha acelerado el potencial de la AM y ha cumplido su compromiso de crear un ecosistema global y abierto que permite a los clientes dirigir su innovación. La compañía también presentó cuatro nuevos materiales incluidos PEEK, nilón de alta temperatura (HTN), HTN-CF25 y HTN-Z (antiestático ESD) diseñados para ofrecer una alta resistencia a la temperatura, sustancias químicas y fatiga, y una robustez extraordinaria en aplicaciones industriales.
Además de presentar la plataforma de impresión HSE 3D de alta temperatura, Essentium anunció la perfecta integración del software de impresión Magics Essentials de Materialise 3D en la impresora Essentium HSE 3D. La integración de software e impresora ofrece un conjunto FFF abierto e integral que incluye un flujo completo con todas las características necesarias para la fabricación en 3D a escala industrial que transformará las plantas de producción.
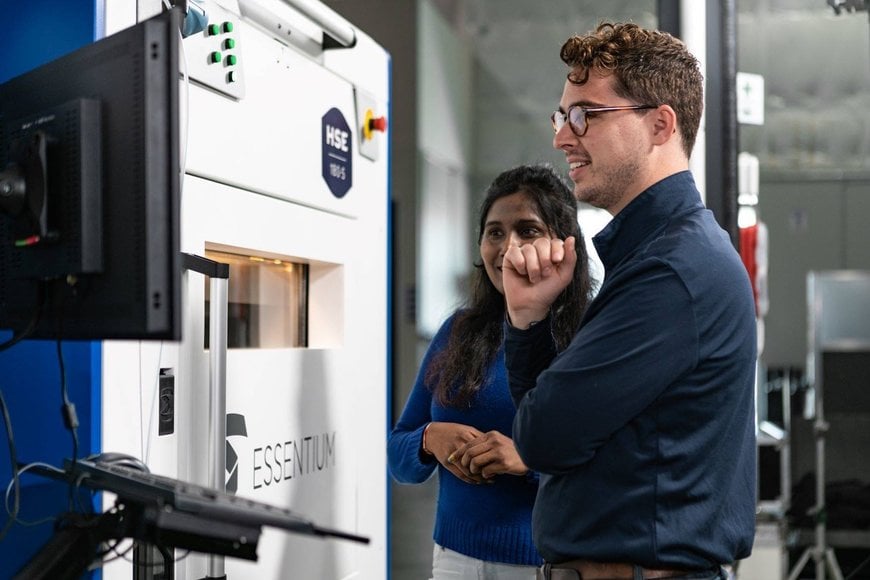
La nueva HSE 180•S HT de Essentium
Renishaw, otra empresa de referencia en el sector, presentó el software de supervisión de proceso acústico InfiniAM Sonic para completar su paquete de software InfiniAM, formado por herramientas de seguimiento AM. Con InfiniAM Sonic los ingenieros pueden detectar los eventos acústicos dentro de la cámara de producción AM y convertir estos datos en información útil acerca de la calidad de la producción. Este software es el primero de este tipo en el segmento AM.
El paquete InfiniAM Sonic está instalado en el sistema RenAM 500Q de fábrica e incluye cuatro sensores de energía acústica para detectar la vibración en la producción. El sistema RenAM 500Q está equipado con cuatro láseres de alta potencia de 500 W para alcanzar ritmos de producción hasta cuatro veces mayores que los sistemas convencionales de un solo láser. En el RenAM 500Q se alcanza la máxima eficiencia ya que los láseres pueden funcionar en toda la placa de producción facilitando el control eficiente de la interacción del láser para garantizar que la calidad no se vea afectada por la interacción de los distintos láseres durante el funcionamiento. Resnishaw colabora también con Sandvik Additive Manufacturing para certificar nuevos materiales AM para aplicaciones de producción. Esto incluye una amplia gama de polvos metálicos constituidos por nuevos compuestos de aleación optimizados para el proceso de fusión de capas de polvo con láser (LPBF) que ofrece unas propiedades superiores de material.
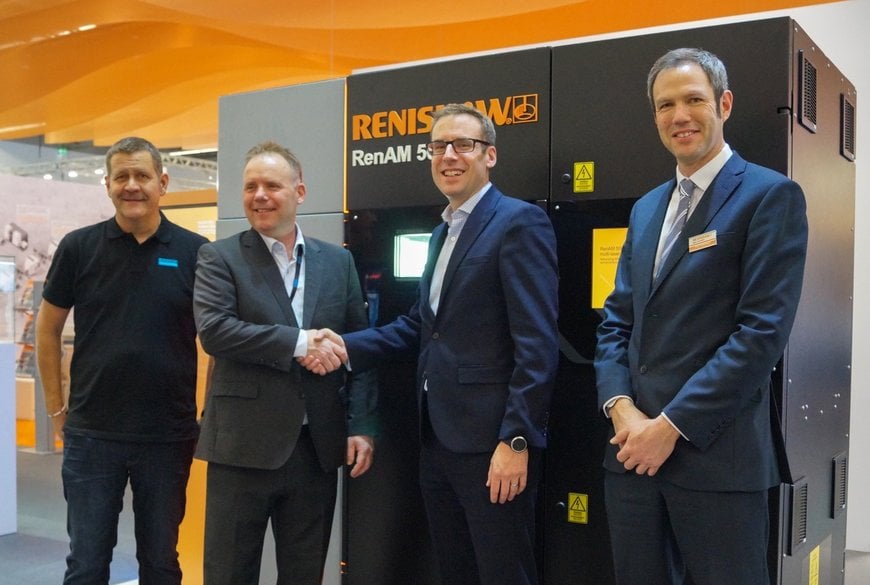
Equipo de Renishaw en Formnext 2019
Si la impresión 3D puede replicar un objeto simplemente escaneándolo e imprimiéndolo, se presenta también una amenaza de seguridad. Se puede simplemente fotografiar o escanear una llave e imprimir un duplicado en cualquier lado. El evento tecnológico que tiene la llave del futuro de la manufactura se clausuró con la entrega de un premio por una llave, no una llave corriente sino la Stealth Key impresa en 3D diseñada y fabricada por UrbanAlps AG, un fabricante suizo ganador del primero premio del desafío purmundus de la feria Formnext 2019. La tecnología furtiva (del inglés Stealth) permitió a UrbanAlps crear una llave física y un cilindro en el que el código está oculto con elegancia en los bordes robustos y finos. Gracias a la imposibilidad de escaneado de la llave mecánica se ofrece la máxima seguridad y un funcionamiento independiente de los sistemas digitales, lo cual permite neutralizar la amenaza y utilizar la misma tecnología con eficacia.
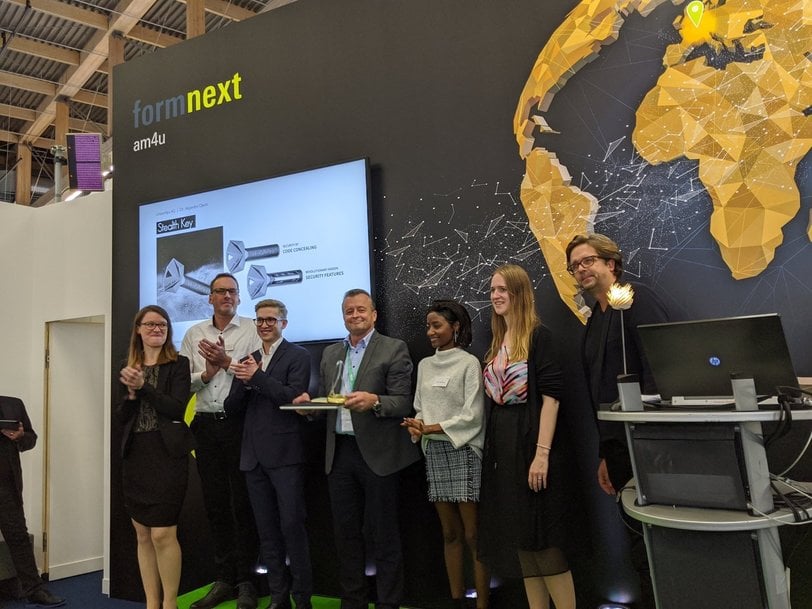
El primer premio del desafío purmundus fue otorgado a la llave Stealth Key
Estos son solo unos cuantos ejemplos de los 852 expositores (frente a los 632 del año anterior) que participaron en la pasada edición de Formnext y que representan toda la cadena de valor añadido. El evento recibió a 34 000 visitantes de 99 países. La comunidad AM crece a escala global.
El camino a seguir
La preocupación cada vez mayor por la degradación del medio ambiente y el cambio climático ha captado finalmente la atención de gobiernos y legisladores, además de las industrias, a escala global. El nuevo mantra es la sostenibilidad, el nuevo objetivo son las emisiones cero de carbono, y más de 60 países persiguen que sus emisiones netas de carbono sean cero en 2050, según Naciones Unidas. A mediados de 2019, Bosch, el proveedor mundial de tecnología y servicios, declaró que la compañía lograría dicho objetivo en 2020 y hay muchas empresas que están aplicando sus propios planes con la misma meta.
Al tiempo que el mundo se mueve hacia la sostenibilidad, la impresión 3D adopta un papel importante sobre todo en los ámbitos de la movilidad. La reducción de peso en todo tipo de medios de transporte terrestre, aéreo y marítimo, es la principal prioridad de los fabricantes OEM. El software de diseño generativo es la tecnología instrumental que lo hace posible. Cuando General Motors rediseñó el soporte de asiento con la tecnología de diseño generativo de Autodesk Fusion 360, el software propuso más de 150 diseños alternativos de los cuales se eligió el más optimizado. Autodesk y BMW están trabajando juntos para utilizar las tecnologías de diseño generativo y los métodos de fabricación aditiva para crear un nuevo tipo de vehículo que sea más ligero, más rápido, más barato, fiable y fácil de fabricar.
La combinación del diseño generativo y la fabricación aditiva tiene un amplio horizonte de aplicaciones más allá de la movilidad. La tecnología ofrece un gran potencial en muchos otros campos donde se utilizan materiales: arquitectura y construcción, edificios y plantas, maquinaria industrial y productos de consumo. Logra aumentar la productividad y ahorrar energía, además de contribuir a reducir la huella de carbono. En cuanto a materiales, la impresión 3D está consiguiendo avances en el mundo de la alimentación, sobre todo en el segmento de la repostería, facilitando la elaboración de diseños atractivos y a la vez complejos de pasteles y bombones.
La rápida evolución y la creciente disponibilidad de la impresión 3D o fabricación aditiva con la reducción de precio de hardware y consumibles harán que el crecimiento sea mayor en los próximos años. La tecnología revoluciona velozmente la forma de diseñar y fabricar desde simple calzado hasta la imponente nave espacial, y ofrece la llave que abre un futuro sostenible.
Autor: Bruno FORGUE